Из чего делают газобетонные блоки: состав, виды, характеристики, плюсы и минусы
экологичность и безопасность состава в Челябинске
Современный газобетон — материал искусственного происхождения семейства ячеистых бетонов, различается типом затвердевания и составом. В статье разбираемся, из чего делают газоблок и безопасен ли его состав.
Составляющие газобетона
Экологически чистый и безопасный для здоровья человека газобетон производится из натурального, дополнительно подготовленного сырья, включая:
- вяжущее вещество — портландцемент;
- порообразователь — алюминиевая паста-суспензия;
- наполнитель — кварцевый песок;
- известь;
- гипс;
- вода.
Строго определенное соотношение компонентов позволяет получать газобетон с характеристиками, необходимыми для заказчика. Наиболее востребован материал промышленного производства, изготовленный на автоматических линиях автоклавным методом.
Важные требования к составляющим для производства газобетона:
- вода должна быть нагрета до +40ºС — +60ºС;
- цемент;
- известь — отвечает за газообразование и белый цвет блоков;
- наполнители — минимальная фракция, отсутствие органического мусора, глинистых примесей, ила.
- Модификаторы — гипс-алебастр, хлористый кальций, жидкое стекло.
Подготовка и подбор состава компонентов
Все продуктысостава, из чего делают газоблоки, проходят предварительное измельчение до нужной консистенции в шаровых мельницах, обработку в шламовых бассейнах. С помощью насосов уплотненный материал поступает в спецустановки для формирования весовых пропорций каждого компонента.
Расчет состава газобетонапроводится в автоматизированных модулях. Исходные материалы смешиваются в широком диапазоне пропорций для получения заданных параметров. Согласно программе, составляющие продукции, предварительно дозированные, перемешиваются в смесителе с портландцементом, известью, алюминиевой суспензией, водой.
Поры автоклавного ячеистого газобетона пронизывают камень насквозь, имеют сферическую форму и размер 1-3 мм. Процентный состав определяется экспериментально и меняется в зависимости от требуемой прочности. Количество вяжущего вещества влияет на прочность бетона: чем больше наполнителя, тем меньше прочность на сжатие.
Замедлить процесс загустения можно с помощью добавки гипса. С помощью соотношения количества извести и алюминия можно регулировать объем газообразного водорода, следовательно, получать продукцию разной плотности.
Преимущества материала
Автоклавный газобетон формируется при высоком давлении в 14 бар и температуре +180ºС. Процесс происходит в автоклавах, загруженных в специальные печи на 12 часов. В результате изделие окончательно затвердевает, образуя структуру искусственного камня. Материал данного вида пожаробезопасен, при нагревании не выделяет вредных веществ. Габариты одного блока равнозначны 20 кирпичам, что сокращает расходы и сроки строительства. Небольшой вес позволяет уменьшить количество работников. Идеальные геометрические размеры обеспечивают совершенно ровные стены. Способность материала аккумулировать тепло помогает создавать комфортный микроклимат в доме. Стойкость к микроорганизмам гарантирует отсутствие плесени и грибка на поверхности блоков.
Завод автоклавного газобетона «Пораблок» выпускает продукцию с отличными технологическими, санитарно-гигиеническими, эксплуатационными параметрами. Высокое качество и соответствие строгим нормативам позволяет использовать изделия в жилищном и специальном строительстве.
Газобетон своими руками в домашних условиях: технология
Газобетон – это универсальный материал, который обладает отменными прочностными характеристиками и является простым в монтаже. Поэтому материал широко применяется в строительстве. Для экономии денежных средств на этом процессе рекомендовано изготовление газобетона своими руками в домашних условиях.
Что такое газобетон и каковы его характеристики
Перед применением газобетона для возведения домов и других построек на участке, рекомендовано предварительно определить его характеристики.
Основные свойства и качества
Соответственно мировым стандартам качества и ГОСТу материал должен обладать перечнем определенных качеств. Качественный материал должен выдерживать 35-100 циклов заморозки и разморозки. Показатель теплопроводности газобетона составляет 0,09-0,38. Плотность материала составляет Д300-Д1200. Средний показатель паропроницаемости – 0,2. Усадка газобетона составляет 0,3 миллиметра на квадратный метр.
Виды материала и изделий из него
Соответственно характеристикам газобетона его разделяют на: теплоизоляционный, конструкционный, конструкционно-теплоизоляционный.
Теплоизоляционный газобетон имеет плотность от 300 до 400. Он имеет низкую теплопроводность и характеризуется незначитекльным весом. Применение материала рекомендуется для теплоизоляции помещений.
Конструкционный газобетон обладает отменными прочностными характеристиками и имеет плотность от 1000 до 1200. Благодаря высокому коэффициенту теплопроводности предоставляется возможность его применения в качестве утеплителя.
Наиболее популярным является конструкционно-теплоизоляционный газобетон. Он характеризуется плотностью 400-900. С его применением возводятся стены и перегородки.
Сильные стороны строений возведенных из газобетона
Материал широко применяется в строительстве благодаря наличию большого количества преимуществ:
- Для производства материала используется песок, известь, цемент, алюминиевая пудра и вода, что обеспечивает экологичность материала.
- Газобетон имеет небольшой вес, что упрощает процесс его укладки.
- Благодаря большим размерам газоблоков ускоряется процесс возведения газобетона.
- Материал характеризуется высоким уровнем стойкости к возгоранию.
- Газобетон является стойким к морозам, что позволяет его применять в суровых климатических условиях.
- Благодаря универсальному составу материала предоставляется возможность его распиловки и шлифовки.
- Газобетон позволяет использовать разнообразные материалы для отделки зданий внутри и снаружи.
- Такие показатели, как прочность и теплопроводность, являются оптимальными.
- Производство материала осуществляется различными компаниями, что позволяет клиенту выбрать наиболее приемлемый вариант для себя.
- Материал обладает паропроницаемыми свойствами, что позволяет обеспечить оптимальный микроклимат в помещении.
- Газобетон обладает хорошими звукоизоляционными свойствами, что обеспечивает комфортное пребывание в помещении.
Газобетонный дом имеет высокие эксплуатационные характеристики, что объясняется большим количеством преимуществ материала.
Недостатки изделий и их устранение
Перед тем, как сделать газобетон в домашних условиях, рекомендовано определить его недостатки. Материал является гигроскопичным, что приводит к усиленному водопоглощению. При отрицательных температурах накопленная в блоках влага кристаллизируется, что приводит к их разрушению.
Для того чтобы решить эту проблему нужно стены из газобетонных блоков облицовывать. С этой целью используется кирпич, металлопрофиль, дерево и другие отделочные материалы.
Производство газоблока своими руками
Технология производства газобетона в домашних условиях требует от мастера придерживаться определенных правил. Этот процесс состоит из нескольких этапов.
Необходимый набор оборудования и материалов
Перед тем, как изготавливать газобетон, нужно подготовить материалы и инструменты. Бетон делается из смеси таких материалов:
- Песок. Рекомендуется отдавать предпочтение кварцевому песку, который предварительно проходит процесс промывки и высушивания.
- Цемент. Высокопрочный материал получается при использовании цемента, который имеет марку более 400.
- Чистой воды.
- Негашеной извести.
- Алюминиевой пудры, каустической соды, сульфата натрия.
Формы
Перед тем, как делают газобетон, подготавливают формы. В строительных магазинах можно купить готовые изделия. Для экономии денежных средств их создают самостоятельно. Изначально изготавливают пенал из деревянных досок. В него вставляют перемычки, с помощью которых обеспечивается разделение каркаса на отсеки. Изготовление форм может проводиться из влагонепроницаемой фанеры. Для того чтобы зафиксировать доски, в них предварительно нужно сделать пропилы.
Размеры ячеек должны совпадать с размерами, которые в соответствии с проектом должен иметь готовый блок. Для того чтобы ускорить производственный процесс, рекомендовано провести одновременное сооружение нескольких форм. Для того чтобы исключить возможность прилипания раствора к формам, их нужно предварительно смазать специальным средством. В домашних условиях рекомендовано применение отработанного машинного масла, которое разводится водой в соотношении 1:3.
Для того чтобы ускорить изготовление газобетона можно использовать мобильные установки, которые состоят из компрессора, смесителя и соединительных рукавов. Предварительно подготавливаются приспособления, с помощью которых удаляются излишки бетона.
Приготовление раствора
Процесс изготовления газобетона в домашних условиях начинается с приготовления раствора. Количество используемых компонентов зависит от того, какой плотности материал пользователь хочет получить. Рассмотри вариант приготовления раствора для газобетона, плотностью 1600 килограмм на метр кубический. Для этого понадобится 1100 килограмм песка и 400 килограмм цемента. Компоненты тщательно перемешиваются. К ним нужно добавить 5 кг извести. Также в раствор добавляются такие добавки, как каустическая сода, алюминиевая пудра и сульфат натрия.
После тщательного перемешивания всех сухих компонентов, они заливаются 189 литрами воды. После перемешивания состава до однородности его можно использовать для заливки.
Заливка
После смазывания форм специальным составом, в них заливается раствор. При этом нужно следить, чтобы формы не заливались до краев, так как при застывании смесь вспучивается и излишки будут вылизать наружу. Формы нужно заливать до половины. После заливки материала наблюдается появление процесса газообразования. На следующем этапе проводится удаление излишков смеси с применением металлических струн. Процедура проводиться по истечению 5-6 часов после заливки.
Спустя 18 часов после заливки можно проводить распалубку изделий. Для того чтобы газобетонные блоки лучше отходили, нужно немного постучать по формам. По истечению месяца газобетон обретет техническую прочность. Затвердевание блоков наблюдается не только в помещениях, но и на открытых площадках.
Сравнение изделий самостоятельного и заводского выпуска
При производстве газобетонных блоков своими руками они затвердевают гидратационно, а на производстве – автоклавно. Эти материалы отличаются между собой по техническим и физическим параметрам. На производстве изготавливаются блоки стационарным и конвейерным способом. При использовании второго варианта снижается необходимость в участии человека к минимуму. В домашнем производстве материала человек принимает постоянное и непосредственное участие.
Рентабельность производства
На рентабельность изготовления блоков влияют разнообразные факторы. Она зависит от:
- Стоимости сырья;
- Вложений на покупку оборудования;
- Количества производственных отходов;
- Желаемого объема;
- Цели производства.
Специалисты провели расчеты в соответствии с показателями, в соответствии с которыми было установлено, что сделать газобетонные блоки своими руками дороже, чем приобрести готовый материал. Кроме того, этот процесс требует затрат сил и времени.
Газобетонные блоки – это универсальный строительный материал, который широко применяется для возведения зданий. Приобрести его можно на заводах и в строительных магазинах. Также можно провести изготовление блоков своими руками, предварительно рассчитав рентабельность этого процесса.
Как делают газобетон — Как это сделано, как это работает, как это устроено — LiveJournal
Всем кто сталкивался со строительством знаком такой материал как газобетон. Несмотря на то, что он считается вполне современным и довольно популярным, история его создания насчитывает более ста лет. Первые попытки сделать пористый искусственный камень были предприняты в конце 19 века, однако они были не очень успешными. Только тридцать лет спустя технология была усовершенствована, и в двадцатых годах прошлого века газобетон стали производить в промышленных масштабах.
Этот строительный материал из Швеции получил название Итонг (Ytong), бренд принадлежит немцам и производит бетонные блоки даже на заводе в России. Именно к ним в гости я приехал в подмосковный Можайск, чтобы выяснить как делают автоклавный газобетон.
Принцип производства газобетона не так сложен как может показаться на первый взгляд и чем-то схож с процессом производства хлеба. Если для производства хлеба необходимы дрожжи для того, чтобы тесто поднялось, так и для производства газобетона используются ингредиенты, благодаря которым бетон увеличивает свой объем, и становится пористым.
Но я начну свой рассказ с самого начала, со склада, где хранится сырье для производства газобетона. Чтобы сделать качественный продукт, нужны качественные ингредиенты, это гипс и кварцевый песок. Кран-погрузчик перемещает своим ковшом сырье в бункер. Оттуда смесь поступает по транспортерной ленте в такой огромный барабан, это шаровая мельница, где сырье измельчают в жидкую суспензию, так как помол идет с водой.
Внутри барабана находятся такие железные шары которые перемалывают все, что туда попадает. Однако со временем шары тоже измельчаются до состояния щебенки, остатки которых отсеиваются вместе со шламом из барабана.
Рядом с мельницей находятся вот такие мешки с железными шарами. Так как это расходный материал, а производство работает в полную мощность, то их требуется довольно много.
Полученное сырье поступает в эти накопительные бункерА на хранение. Здесь может хранится несколько сотен тонн готовой смеси из цемента, извести и песка. Затем в газобетоносмесителе происходит смешивание всех компонентов. Для производства газобетона используется 60% кварцевого песка, 20% цемента, 20% извести, 1% алюминиевой пасты и вода.
Алюминиевая паста и вода добавляются непосредственно перед заливкой к уже смешанным компонентам. Готовая смесь заливается примерно на 2/3 в специальную прямоугольную форму, стенки которой не имеют жесткого соединения с дном. Все происходит довольно быстро.
Именно на этом этапе происходит самое интересное. Алюминиевая паста вступает в реакцию с известью, в результате чего выделяется водород. Он в течении нескольких часов образует в сыром бетоне огромное количество пор размером от 0,5 до 2 мм, равномерно распределённых внутри, но в процессе схватывания летучий водород в порах замещается воздухом.
После заливки формы со смесью медленно продвигаются в помещение с высокой влажностью и температурой. Как мне сказали специалисты, здесь может быть до 60 градусов тепла. Когда я снимал эти кадры, то чувствовал себя как в бане. Хотя по сути это и есть баня, правда только для газобетона. В этом помещении смесь находится до тех пор, пока не увеличится в объеме до верхней кромки формы. На это уходит от четырех до 5 часов.
Затем форма выкатывается из бани и вакуумный кран переносит застывшую смесь на следующий этап, причем содержимое без дна удерживается только за счёт вакуума.
На место, куда должна будет опуститься форма укладывается решетка и закатывается такой аппарат для нарезки газобетона на блоки равного размера. Нарезка производится с помощью струн. После этого сверху и с боков срезается слой, чтобы поверхность блоков была ровной без шероховатостей. Остатки и крошки сдуваются сжатым воздухом.
Затем кран захватывает решетку с блоками и переносит их на следующий этап производства. Тут же сразу укладывается новая решетка в основание для следующей партии блоков. Производство на заводе полностью автоматизировано, сотрудникам остается только контролировать процесс и следить за качеством.
Теперь блоки нужно поместить в автоклав. Поддоны с сырыми блоками укладываются в три уровня, после чего с помощью таких платформ отправляются в автоклавные камеры, где они в течение 12 часов при повышенном давлении обрабатываются насыщенным паром при температуре 190°C. При этом температура в начале и конце цикла плавно поднимается и опускается в течение определённого времени. Каждый автоклав имеет длину более 30 метров. Их использование позволяет повысить прочность газобетонных блоков и уменьшить его последующую усадку, стандарт в таком случае менее 1 мм на метр.
После этой процедуры блоки имеют влажность порядка 30%, которая постепенно, в течение года упадёт от 5-10%. Автоклавирование это очень важный этап, улучшающий свойства газобетонных блоков. Если до попадания в автоклавы блоки были серыми, то после того, как их оттуда достали они становятся белыми.
Каждая партия блоков после автоклавирования отправляется в лабораторию для проверки на соответствие заданным характеристикам. Затем готовые блоки отправляются на линию упаковки.
На этом этапе тоже все автоматизировано, робот укладывает палету и помогает запечатывать ряды блоков пленкой, после чего они отправляются на склад, который расположен под открытым небом, здесь всегда есть запас выпускаемой продукции. Основная продукция завода это блоки толщиной от 50 до 500 мм с плотностью от 400 до 600 кг/куб.м.
Следует упомянуть еще несколько важных фактов о заводе. Отходы производства или брак заново перерабатываются, а при помоле сырья и заливке блоков применяется конденсат от автоклавов. Предприятие не сбрасывает производственных сточных вод, и в производстве используется водооборотная схема, вся вода от охлаждения машин и промывки оборудования используется в замешивании сырьевой смеси. Получается практически безотходное производство.
Газобетон легко обрабатывается: пилится, сверлится, строгается обычными стальными инструментами. В него легко забиваются гвозди, скобы, установочные изделия. Блоки из газобетона имеют относительно небольшую плотность и массу.
Стандартный блок для строительства частного дома 625х250х375 D400, массой 26кг может заменить в стене до 26 кирпичей общей массой до 138кг. При этом газобетонный блок является конструкционно-теплоизоляционным материалом, т.е. обладает свойствами как несущих элементов-кирпичей, так и теплоизоляции. Стены дома из данного материала не требуют утепления. Трудоемкость кладки блоков из ячеистого бетона в 5–7 раз ниже, чем у кирпича.
Теперь и вы знаете, как делают газобетон!
Если у вас есть производство или сервис, о котором вы хотите рассказать нашим читателям, пишите на адрес ([email protected]) и мы сделаем самый лучший репортаж, который увидят тысячи читателей сайта Как это сделано
Отдельные фото из моих репортажей можно смотреть в инстаграме инстаграме. Жмите на ссылки, подписывайтесь и комментируйте, если вопросы по делу, я всегда отвечаю.
Также на ютюбе выходят мои интереснейшие ролики, поддержите его подпиской, кликнув по этой ссылке — Как это сделано или по этой картинке. Спасибо всем подписавшимся!
Газобетонные блоки — практически идеальный строительный материал
Газобетонные стеновые блоки представляют собой изделия, сделанные из ячеистого бетона. Из чего же состоит газобетонный блок? Для его изготовления берется кварцевый песок, вода и цемент, присутствуют дополнительные компоненты. Блоки делаются в специальных печах, где обеспечено высокое давление и температура.
Что такое газобетон
Этот материал легкий и прочный, но обладает отличными свойствами, в том числе, плотностью и прочностью, теплопроводностью. Многие строители считаются газобетонные блоки идеальными, когда речь идет о строительстве до четырех этажей. Они отлично подходят при возведении стен и перегородок, в монолитном строительстве блоками этой категории можно заполнять проемы.
Газобетон был изобретен давно, но с разработкой новых современных производственных технологий, стали выпускаться усовершенствованные газобетонные блоки различных конструкций и видов.
Состав газобетонных блоков
Производятся современные газобетонные блоки из песка и извести, цемента, алюминиевой пудры. Токсичных веществ готовый материал не выделяет, поэтому по характеристикам его часто сравнивают с деревом.
При том, что блоки имеют дополнительные плюсы – не гниют и не подвержены естественному процессу старения. Материалы, которые входят в состав блоков, экологически чистые. Радиационный фон готового изделия не превышает 11 мкр/ч.
Благодаря простому составу блоки получаются пористыми, поэтому строение будет постоянно дышать пропускать воздух в помещение, от чего находиться в нем будет приятно и комфортно.
Из чего делают газобетонные блоки:
- Смеси цемента и извести;
- Кварцевого песка;
- Алюминиевой пудры;
- Воды;
- В зависимости от особенностей производства могут добавлять смеси, улучшающие свойства газобетона.
Газобетон представляет собой пористый строительный материал, который, чаще всего, прессуется в виде блоков. Главным компонентом для производства является цемент в сочетание с известью, также песок.
Пенобетон и газобетон: существенные отличия
Часто газобетон сравнивают с пенобетоном, более того, эти материалы могу путать. На самом деле они сильно отличаются друг от друга по компонентам, способу производства и основным характеристикам.
Пенобетон — это более дешевый материал, при производстве которого вместо кварцевого песка используются производственные отходы. Пенобетон дозревает на воздухе, а это значит, у него более низкие эксплуатационные качества.
Блоки газобетона будут иметь коэффициент теплопередачи гораздо выше. Поэтому уровень теплоизоляции в готовом строение также будет выше. В среднем при толщине стен от 400 мм от уже будет равен принятым средним показателям.
Газобетон не дает усадку в процессе эксплуатации, а вот от пенобетона усадки надо ожидать. Из всего сказанного становится понятным, почему пенобетон дешевле описываемого материала на 20-25%. Но при покупке более дешевого материала также возрастает риск купить некачественный пенобетон, который в итоге придется заменять более надежными материалами.
В пенобетоне поры распределены не равномерно, они также отличаются по размеру. Также более углубленное внешнее изучение материалов показывает, что первый практически не имеет отклонений в геометрии, а во втором случае такие отклонения могут достигать 10 мм.
Отличать также можно по внешнему виду. Газобетонные блоки по цвету всегда белые, а вот пенобетон более темный и серый. Если разрезать первый вид блока, то будет видна упорядоченная пористая структура и каждая ячейка в точности повторяет другую.
На основании этого можно сделать вывод, что газоблоки все же лучше, чем пеноблоки, хотя и существенно дороже, но за качество всегда приходится платить больше.
На фото идеальная кладка из газобетонных блоковПлюсы газобетонных блоков и их минусы
Основные свойства описываемого материала настолько хороши, что являются важными его плюсами:
- Прочностью и долговечность. Чтобы эти характеристики проявились в полной мере, важно использовать материал правильно: для возведений зданий без каркаса и высотой не более четырнадцати метров. Также его можно смело применять для устройства внутренних стен и перегородок. По сроку службы блоки этого вида можно приравнивать к сроку службы кирпичей. Производитель дает гарантию в 80 лет.
- Качественная теплоизоляция. В многочисленных порах материала заключен воздух, что обеспечивает отличные свойства по сбережению тепла. Всем строительным нормам дом из газобетонных блоков полностью соответствует. Чем ниже объемный вес газобетона, тем выше будут теплоизоляционные характеристики. Прогреваются дома из описанного вида блоков всего за несколько часов.
- За счет общей легкости блоков нагрузка на фундамент сводиться к минимуму. Один блок заменяет при кладке двадцать кирпичей, это значит, что общее время работ и расход материала сокращается в несколько раз.
- Экологичность. Материалы основные только натуральные и чистые, сам по себе блок также показывает высокие экологические свойства. Вредных веществ он не выделяет. По способности пропускать воздух газобетон сравнивается с деревом. Стены из описываемого материала на ощупь всегда теплые за счет низкой теплопроводности.
- Устойчивость к огню. Проведенные исследования показали, что материал горение не поддерживается, так же, как и сам не горит. На газобетонную стену прямой огонь может воздействовать 3-7 часов и она устоит. Часто блоки этой категории используют, чтобы защищать от огня металлические конструкции.
- Морозостойкость, то есть, способность выдерживать полное замораживание и оттаивания. Мелкие поры материала вытесняют лед и воду. Поэтому около ста циклов сохранность газобетонного блока обеспечена. Если сравнить с кирпичом, он выдерживает только 25 циклов, а пенобетон – всего 35 циклов).
- Удобство обработки. Блоки из описываемого материала можно смело сверлить, колоть и резать. Причем, разрезаются блоки с помощью обычной ручной пилы.
Но любой строительный материал наравне с преимуществами имеет и свои недостатки. Его говорить про газобетон, то тут есть такие свои нюансы. Во-первых, не рекомендуется стоить здание выше трех этажей, потому что материал имеет ограниченную способность к сжатию. Во-вторых, требуется дополнительная внешняя облицовка стен, потому что материал активно впитывает влагу. К третьему минусу относится высокий коэффициент усадки (особенно, у неавтоклавного варианта).
Практически все характеристики описываемого материала являются отличными для строительства. Особенно надо обращать внимание на прочность, из-за которой газобетонные блоки лучше всего использовать для возведения построение не более четырех этаже в высоту.
Как выбрать качественные газобетонные блоки
При подборе стройматериалов важно знать и учитывать такие параметры как теплопроводность, плотность, прочность, звукоизоляция, огнестойкость.
При покупке важно сравнивать эти характеристики, потому что у разных производителей они могут отличаться:
- Коэффициент теплопроводности должен начинаться от 0,075 Вт/(м•К) для блоков плотностью D350 и от 0,25 Вт/(м•К) для блоков марки D700. В доме будет теплее, когда у используемого материала показатель этого коэффициента будет низким.
- Плотность в отношении массы к объему определяется марками от D300-350 до D1200 кг/м?. Чем выше показатель, тем более прочной будет конструкция, более хорошей будет звукоизоляция.
- Любые блоки этой категории должны обладают огнестойкостью, потому что они относятся к материалам негорючим. Перегородка из ячеистого бетона, уже отштукатуренная, в течение нескольких часов может выдерживать огонь не изменяя свой изначальный вид, не утрачивая характеристики.
- Газобетон должен быстро выветривать влагу и выводить водяной пар из помещения, которое отапливается.
Чем выше индекс воздушного шума (определяется в дБ), тем лучшими звукоизоляционными свойствами обладает материал.
С появлением на рынке стройматериалов ячеистых бетонов расширились возможности застройщиков. Те уникальные свойства, которые присущи газобетону, грех не использовать при строительстве жилых и специальных объектов.
Есть ли вред для здоровья
Газобетонные блоки – это совершенно безвредный для здоровья человека материал. Несмотря на то, что материал этот искусственный, он производится из природных компонентов, которые являются совершенно безопасными. Экологичность придают те природные компоненты, из которых блоки состоят.
Этот материал активно используется в современном строительстве, он имеет несущественные минусы. Его можно смело использовать для зданий до четырех этажей высотой. Высота здания не имеет значения, если делать перегородки и несущие стены внутри помещения.
Возведение построек из газобетона сопряжено с некоторыми особенностями. Перед началом работ следует внимательно изучить не только свойства газобетона, но и технологию его укладки. Газоблоки укладываются намного проще, чем кирпичи или шлакоблок.
виды, изготовление в домашних условиях, видео
Газобетон – это искусственный камень, который используют для возведения стен в индивидуальном строительстве. Он подходит для сооружения несущих конструкций, внутренних перегородок и заполнения межкаркасных пространств. Газоблоки не дают большой нагрузки на фундамент, поскольку имеют ячеистую структуру и малый вес. Это экономичный стройматериал, обладающий высокими теплоизоляционными свойствами.
Оглавление:
- Особенности и виды стройматериала
- Пропорции компонентов
- Методика производства своими руками
Состав и способ получения газобетона
Существует несколько типов классификации ячеистого бетона: в зависимости от назначения, формы, технологии производства и состава.
1. По способу обработки различают автоклавный и неавтоклавный газобетон.
2. По назначению газоблоки могут быть теплоизоляционным, конструкционным или конструкционно-теплоизоляционным. Они имеют определенную маркировку, например, газобетон d500 относится к классу конструкционно-теплоизоляционных блоков.
3. По форм-фактору делятся на U-образные, прямые и паз-гребневые.
Газоблоки изготавливают из песка, цемента, извести, воды, гипса и алюминиевой пудры. Также в производстве могут использоваться вторичные и побочные промышленные материалы, такие как шлак и зола. В зависимости от состава газобетона, его классифицируют на:
- цементный;
- шлаковый;
- известковый;
- зольный;
- смешанный.
В искусственно синтезированный камень строительная смесь преобразуется лишь при определенных условиях. Для его получения используют технологию автоклавного затвердения. В этом случае состав застывает под влиянием насыщенного пара и высокого давления, меняя свою структуру. В смеси образуется минерал тоберморит, который придает материалу прочность. Таким образом получают автоклавный газобетон.
Бетон, затвердевающий в естественных условиях, называют неавтоклавным. Он имеет ячеистую структуру, но отличается по своим свойствам от газоблоков, изготовленных по специальной технологии. Этот стройматериал больше подвержен усадке при эксплуатации, поэтому его целесообразно применять в случае небольших нагрузок. Чтобы увеличить прочностные характеристики неавтоклавных блоков, в исходный состав добавляют различные армирующие вещества и наполнители. Снизить усадочную деформацию позволяет применение полиамидных пластмасс при армировании.
Производство неавтоклавных блоков не требует дорогостоящего оборудования, поэтому их можно сделать самому.
Газобетон своими руками
Процесс производства состоит из нескольких этапов:
- подбор и смешивание компонентов;
- заполнение форм раствором;
- выдержка состава для набора прочности;
- извлечение из форм.
В универсальном составе для получения газобетона содержится цемент, песок, известь, алюминиевая пудра. Исходные добавки и их пропорции могут меняться, в зависимости от наличия сырья и требований к готовому стройматериалу. Например, в автоклавном производстве песок иногда заменяют золой или шлаком. А для получения стройматериала с меньшей плотностью можно делать газобетоны на основе смол ТЭС.
При изготовлении газобетона в домашних условиях необходимо правильно рассчитать соотношение расходных материалов и учесть особенности укладки и погрешности замеров. Но существуют и стандартные рецепты смеси для газоблоков, в которых указаны следующие пропорции:
- Цемент – 50-70 %;
- Вода – 0,25-0,8 %;
- Газообразователь – 0,04-0,09 %;
- Известь – 1-5 %;
- Песок – 20-40 %.
Данные вещества используются и при автоклавном производстве. Ориентируясь на приведенное в рецептуре соотношение, можно рассчитать приблизительное количество компонентов, которые войдут в состав на 1 м3 газобетона:
- Портландцемент – 90 кг;
- Вода – 300 л;
- Газообразователь – 0,5 кг;
- Известь – 35 кг;
- Песок – 375 кг.
Однако идеального состава в домашних условиях можно добиться лишь опытным путем, поскольку многое зависит от качества исходных компонентов. Повлиять на течение химической реакции может как температура воды, так и марка цемента.
Инструкция по самостоятельному изготовлению неавтоклавного газобетона
Для получения газоблока дома не потребуются сложная аппаратура и инструменты. Главное – четко следовать пунктам приведенного ниже пошагового руководства и использовать компоненты в определенном соотношении, а не «на глаз».
1. Исходя из указанных пропорций вычислить необходимое количество ингредиентов.
2. В первую очередь, необходимо смешать портландцемент с предварительно просеянным песком.
3. В полученную смесь влить воду и все тщательно перемешать.
4. Добавить в раствор другие компоненты. Алюминиевая пудра всыпается в последнюю очередь. В приготовлении как неавтоклавного, так и автоклавного газобетона одинаково важен процесс смешивания ингредиентов. Для равномерного распределения воздушных пузырьков лучше использовать бетономешалку.
5. Полученный раствор разливается в специальные формы, которые изготавливаются из металлических листов или деревянных досок. Чтобы застывший газобетон было легче достать, лучше использовать разборные конструкции. Кроме того, форму рекомендуют смазывать машинным маслом, разведенным с водой.
6. Заливать смесь нужно наполовину, поскольку она в процессе химической реакции расширяется практически вдвое. Этот процесс занимает около шести часов, после чего можно выравнивать блоки, срезая выступившую массу.
Формирование в этом случае длится дольше, чем для автоклавного газобетона – требуется не менее 12 часов, чтобы смесь затвердела. Для ускорения процесса застывания состава рекомендуют добавить растворимые соединения натрия (соду) на этапе приготовления раствора. Марочную прочность материал набирает после 28 дней выдержки. Готовый неавтоклавный газоблок, приготовленный своими руками, подходит для малоэтажного строительства, например, для возведения одноэтажного дома или гаража.
Газобетонные блоки своими руками в домашних условиях
Значительно уменьшить финансовые затраты на строительство жилья можно, если сделать газобетон своими руками в домашних условиях. Газобетонные изделия в строительстве применяются очень часто.
Из них легко возвести самые разные постройки с большой экономией раствора.
Что такое газобетон
Газобетонные строительные блоки могут быть разного размера и формы. Но состав их практически всегда одинаков. Газобетонные блоки своими руками можно сделать из:
- цемента высокого качества;
- извести;
- кварцевого песка;
- гипса;
- алюминиевой пудры;
- воды.
Технология производства этого материала довольно проста. Производить газобетон можно во дворе своего дома или непосредственно на строительной площадке. Готовые блоки — это параллелепипеды из пористой бетонной массы, в которой находится множество мелких воздушных пор. Они имеют размеры около 3 мм. Образуются поры за счет добавки в раствор алюминиевой пасты или пудры. Иногда в состав кроме перечисленных компонентов добавляются еще некоторые вещества в очень малых количествах. Они нужны для изменения некоторых параметров стройматериала.
По способу производства газобетон может быть сделан автоклавным и неавтоклавным способом. Первый способ не подходит для домашних условий. Для него необходимо дорогостоящее оборудование. Неавтоклавный способ более простой, он позволяет наладить производство газобетона своими руками дома. При изготовлении применяется реакция воды с алюминиевой пудрой, в результате которой выделяется огромное количество углекислого газа, который образует поры внутри блоков. Масса через некоторое время затвердевает. Происходит это в естественных условиях. Тело блока получает множество пор от 1 до 3 мм в диаметре.

Мини-завод по производству неавтоклавного газобетона
Пористая структура — это главное преимущество газоблока. Поры делают материал легким, наделяют его высокими теплоизоляционными свойствами. Плотность для газобетона держится на уровне 300-1200 кг/м³. Чтобы поры прочно держались в бетоне, он должен быть помещен в прочную форму, которая задает размер будущему блоку. Масса твердеет за 2 часа. После этого блоки можно вынимать из формы и раскладывать на стеллажи для полного завердения. Окончательная прочность формируется только на 28 день естественной просушки блоков.
Изготовление газобетона своими руками
Производство газобетона в домашних условиях требует наличия некоторых инструментов. Необходимо подготовить:
- болгарку с диском;
- ножовку по дереву;
- электрическую дрель;
- рубанок;
- ножовку для работы по металлу;
- острый нож;
- слесарный молоток;
- лопату для раствора;
- миксер для замешивания смеси;
- линейку;
- строительный фен;
- мастерок,
- стальную струна для обрезки блоков;
- шпатель;
- весы;
- зубило и стамеску;
- мерное ведро.
С помощью мерного ведра и весов отмеряются необходимые компоненты для раствора. Производство газоблоков осуществляется из следующих компонентов:
- портландцемент марки М400-М500 — 50-70%;
- просеянный кварцевый песок — от 20 до 40%;
- известь в качестве пластификатора — 1-5%;
- пудра или паста алюминиевая — 0,04-0,09%;
- вода — 0,25-0,8%.
-
- Разборная металлическая форма
-
- Заливка легкого бетона
-
- Удаление излишков бетонного раствора
-
- Блоки после распалубки
Смесь тщательно перемешивается и раскладывается в формы, которые бывают разные. Это может быть довольно прочный ящик. Высота его равняется высоте блоков. Общий объем — 4-9 газоблоков. Сделаны формы могут быть из дерева или металла. Конструкцию желательно изготовить разборной. Более сложный вариант — короб с ячейками, который может быть выполнен из дерева толщиной 30-40 мм, или из металла 4-6 мм. Внутренние перегородки можно сделать из фанеры. Толщина ее должна быть 12-15 мм. Перед заливкой раствора поверхности изнутри нужно смазать техническим маслом и прогреть всю конструкцию феном до 40˚. Смесь заливается до уровня половины высоты короба. Остальное пространство заполнится при расширении состава и образовании пор.
Реакция выделения газа длится 6-8 минут. Раствор сначала поднимается, затем слегка садится. После усадки можно верхнюю часть срезать заготовленной струной, блоки вынуть из формы. Охлаждение блоков должно происходить в естественных условиях. Применение вентиляторов не рекомендуется. Установка формы рекомендуется на ровной горизонтальной поверхности. Лучше подготовить сразу несколько коробов, чтобы замешивать значительное количество раствора. Рабочая площадка должна быть укрыта от ветра и осадков. Размеры блоков можно выбрать по собственному усмотрению.
Заключение по теме
Как сделать газоблоки в домашних условиях? Возможен ли такой вариант? Из чего их делать? Ведь нужна особая аппаратура и оборудование для изготовления газобетона в домашних условиях. Построить стены домов можно с гораздо меньшими затратами, если сделать газоблоки самостоятельно. Специального оборудования требуют лишь строительные материалы автоклавного способа изготовления. Таким способом делают материалы из бетона на производстве. Дома можно готовить блоки только неавтоклавным способом. Для этого нужен качественный портландцемент, песок с минимальными примесями глины, известь, вода, алюминиевая пудра и некоторые другие вещества для изменения характеристик готового изделия.
Смесь хорошо перемешивается и заливается в формы, которые тоже можно изготавливать своими руками. Через 2 часа верхушки блоков срезаются металлической струной, сами блоки вынимаются и раскладываются для сушки. Окончательная сушка длится 4 недели. К этому времени блоки приобретают настоящую прочность. Для производства газобетона на 1 м³ блоков требуется 90 кг цемента, 300 л воды, 0,5 кг алюминиевой пудры, 35 кг извести и 375 кг песка. Это приблизительный состав.
Газобетонные блоки — материал для строительства стен. Он обладает высоким качеством и прочностью. Широко применяется в малоэтажном строительстве. Для возведения собственного дома вполне возможно сделать блоки своими руками.
Газобетонные блоки своими руками: технология производства
Многие владельцы загородных домов с целью сэкономить изготавливают газобетон своими руками в домашних условиях. Газобетонные блоки пользуются большим спросом среди застройщиков, поскольку обладают отличными эксплуатационными характеристиками. Но чтобы домашний строительный материал был качеством не хуже заводского, нужно ознакомиться со всеми особенностями его изготовления заранее, уделив особое внимание пропорциональному соотношению компонентов в составе.
Что собой представляют?
Востребованный в современное время строительный материал — газобетон нашел широкое применение при сооружении различных зданий. Изначально его изготавливали исключительно в заводских условиях, но позже опытные застройщики стали осуществлять производство газобетона собственноручно. Сам процесс выпуска газоблоков несложный, однако, требует строгого соблюдения технологического процесса и пропорций для замешивания. По классу газобетон относится к ячеистым бетонам, содержащим в структуре поры-ячейки.
Сильные и слабые стороны
Этот стройматериал имеет немалое количество преимуществ, которые значительно преобладают над недостатками. А считают плюсами газобетонных блоков следующее:
- Высокая прочность.
- Легкий вес.
- Отличные теплоизоляционные свойства. Здания из этого материала не требуют дополнительного использования теплоизоляционных средств, что существенно сэкономит бюджет.
- Поглощает уровень шума, проникающий извне.
- Универсальность.
- Влагостойкость и морозостойкость.
- Безопасность. Имея натуральный состав, является безопасным для здоровья человека.
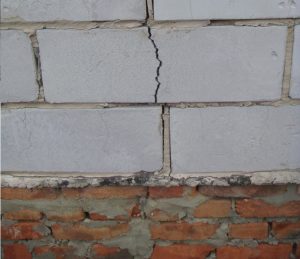
Из недостатков выделяют повышенную хрупкость, теплопроводность и способность чрезмерно поглощать влагу. Из газобетонных блоков можно построить ограждения, перегородки, наружные одно-, двух- и трехслойные стены, а также несущие внутри помещений. Следует отметить, что газобетон бывает 2 типов:
- Автоклавный. Газобетон изготавливается путем термической обработки стройматериала под давлением в специальных печах, которые носят название автоклав.
- Неавтоклавный. Газобетонные блоки твердеют и прочнеют в естественных условиях.
На дому удастся изготовить только неавтоклавный стройматериал, но при правильном соблюдении технологического процесса блоки выйдут не менее прочными и качественными.
Инструменты и материалы
Оборудование
Чтобы сделать газобетон собственноручно на дому, нужно запастись следующим оборудованием:
- Металлические струны. Они необходимы для удаления вытекающего газобетонного раствора.
- Формы. Применяются для придания изделию необходимого геометрического размера.
- Бетоносмеситель. Смешивает компоненты раствора и соединяет готовую массу с газообразователем. Без него не получится сделать качественный и правильной консистенции строительный материал.
Составляющие
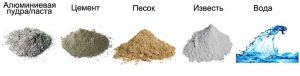
От правильности приготовления раствора зависит прочность газоблоков и непосредственно возводимого сооружения. Ингредиенты берутся только высококачественные, строго в соответствии с необходимой дозировкой. Так, понадобится 1 т портландцемента, маркой не ниже М400, 180 кг кварцевого песка, 1,5 кг каустической соды, 400 г алюминиевой пудры и в среднем 60 л воды. Подготовив компоненты, можно приступать к изготовлению газобетона, следуя такому алгоритму:
- Смешать цемент и песок.
- Влить воду и размешать смесь.
- Всыпать постепенно остальные составляющие (кроме серебрянки), постоянно помешивая массу.
- Подмешать алюминиевую пудру. Именно она вступает в реакцию с известью и в результате получается водород. Он и образует в сырье, имеющее невероятное множество пор.
Подготовка форм
Еще один важный этап производственного процесса — изготовление форм. Их можно приобрести готовые либо сделать собственноручно. Выбрав второй вариант, потребуется взять доски и сколотить из них прямоугольную емкость. В нее вставить перемычки, разделяющие форму по всей длине на ячейки. Размерами этих ячеек определяются параметры газобетонных блоков. Чтобы раствор не прилипал к доскам, опытные застройщики рекомендуют смазывать их внутренние части масляным составом, который готовится из 3 частей воды и 1 части машинного масла.
Технология производства
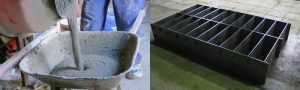
Автоклав — специальное оборудование, которое нагревает раствор под давлением выше атмосферного. С его помощью удастся создать прочный, высококачественный строительный материал, но применение такого агрегата возможно только в заводских условиях. Дома же при приготовлении газобетона приходится обходиться без такого оборудования и после того, как раствор размешан, а формы подготовлены, приступают к заливке. Этот этап обычно сложностей не вызывает, но также требует определенной аккуратности и внимательности. Подготовленный газобетон вливают в емкости, заполняя их наполовину, поскольку после химической реакции раствор начнет подниматься. Далее идет обратный процесс и строительная смесь опускается.
Чтобы придать газобетонным блокам ровную поверхность, нужно срезать выступающий бугорок металлической струной и оставить бетонное изделие высыхать, набираться прочностных характеристик. Спустя 24 часа блоки извлекают и ставят на ровный участок, пока они полностью не затвердеют. При этом нужно следить, чтобы в помещении, где сохнут газоблоки, не было сквозняков.
Газобетонные блоки из автоклавного сплава |
Блоки AAC: газобетонные блоки из автоклавов
Krishna 26 апреля 2017 г. ТЕХНОЛОГИЯБлоки AAC легкие Блоки из пенобетона для автоклавов . Он производится путем реакции алюминия и пропорциональной смеси извести, цемента и летучей золы. Во время этого процесса выделяющийся газообразный водород создает миллионы крошечных ячеек с воздухом, создавая сильную ячеистую структуру AAC. Блоки AAC дополнительно укрепляются путем отверждения паром под высоким давлением в автоклавах.Сформованный таким образом продукт не только легкий, но и имеет более высокую прочность на сжатие.
Плотность этих легких блоков AAC обычно находится в диапазоне 550 — 650 кг / м³ . Что превосходит большинство типов легких блоков. Блоки AAC на 25% прочнее других изделий той же плотности.
Газобетонные блоки с автоблокировкой являются новинкой в гражданской промышленности. Он заменяет нынешнее использование красного кирпича. Так как у него много особенностей по сравнению с традиционным красным кирпичом.Вы можете узнать о некоторых из них ниже.
[NO_TOC]Преимущества блоков AAC:
- Номинальный размер блока AAC 9 ″ X 8 ″ X 4 ″ -12 ″
- По сравнению с объемом обычного красного кирпича с кирпичом AAC
Объем 1 кирпича AAC = Объем 7 красных кирпичей для (9 ″ X 8 ″ X 4 ″)
- Блок AAC имеет вес 9–12 кг в зависимости от условий влажности. По сравнению с красным кирпичом снижается на 60% статическая нагрузка на конструкцию.
- Это не только уменьшает постоянную нагрузку на конструкцию. Это также снижает стоимость использования стали и бетона в конструкции.
- Соединительные кирпичи AAC экономичны. Как уже упоминалось, 1 кирпич AAC = 7 кирпичей. Для соединения 7 красных кирпичей друг с другом требуется больше раствора для соединения по сравнению с соединением одного блока AAC с другим.
- Прочность на сжатие блока AAC выше 5-6 Н / кв.м, тогда как у красного кирпича прочность на сжатие составляет 3,50 Н / кв.м.мм
- Огнестойкость: Они обеспечивают хорошую огнестойкость от 2 до 6 часов в зависимости от размера. Чт
Кладка домов из ячеистых (газобетон и пенобетон) стеновых блоков | Своими руками
Термин «ячеистый бетон» практически не используется в повседневной жизни. Многие частные разработчики понятия не имеют, что это значит. А вот газобетон и пеноблоки всем хорошо известны, ведь их везде используют на стройках любого масштаба и статуса.
Их «одноклассник» пенополистирол — не так известен, но тоже занимает достойное место на строительном рынке.Эти материалы объединяют схожую пористую структуру, образованную мельчайшими «пузырьками воздуха» — ячейками. От них и пошло «классное» название — ячеистый бетон, о котором можно прочитать в специальной литературе или, скажем, на страницах нашего журнала.
Блоки с «воздушными кошельками»
Воздух превращает холодный и твердый бетон в теплый, легкий и податливый, но в то же время достаточно прочный стеновой материал. По плотности и теплотехническим показателям газо- и пеноблоки близки к дереву.Но этим сходство с деревом не ограничивается. Строительные изделия из ячеистого бетона паропроницаемы (то есть «дышат»), и в целом с точки зрения экологии безупречны.
Блоки легко обрабатываются ручным инструментом. Более того, их можно сковать специальной теркой, например, чтобы скруглить стену или аккуратно сгладить выступающий угол. В отличие от дерева, стеновые материалы этого класса не реагируют на изменение влажности, не гниют и не горят (кроме полистиролбетона, смешанного с полимерными «зернами»).
Помимо общих качеств изделий из ячеистого бетона, существуют существенные отличия, которые следует учитывать при выборе того или иного изделия. И сделать это нужно еще на этапе планировки строительства загородного дома.
НАШ СОВЕТ
Блоки из ячеистого бетона средней плотностью до 400 кг / м3 (пористость — 92%, класс прочности на сжатие не ниже В 0,35) могут использоваться только в качестве утеплителя.
Самонесущие стены в домах на основе монолитного каркаса возводятся из теплоизоляционных конструктивных элементов (плотность -700 кг / м 3 , пористость — до 82%, класс прочности на сжатие не ниже В 1,5). ,
А вот коттеджи с несущими ограждающими конструкциями и перегородками возводятся из конструкционного ячеистого бетона (плотность -800-1100 кг / м 3 , пористость — до 68%, класс прочности на сжатие не ниже В 3,5).
НАША ССЫЛКА
Блоки из ячеистого бетона отлично вписываются в концепцию энергосберегающего и даже пассивного дома, то есть конструкции, для обогрева которой требуется минимум энергоресурсов. Блочные стены толщиной 400-500 мм облицовываются специальными теплоизоляционными плитами и строится кирпичный фасад — декоративная стена из облицовочного кирпича.Между нагревателем и внешним экраном оставляется воздушный зазор (для выдерживания конденсата). Такие ограждающие конструкции (вместе с современными оконными блоками и правильно устроенной хорошо утепленной системой кровли) отлично сохраняют тепло.
Читайте также: Стена из газоблоков своими руками
Благородное происхождение
Газобетонные блоки производят крупные промышленные предприятия с хорошо организованной технической базой (YTONG, XELLA, Hebel, Германия, Липецкий завод строительных изделий, Клинцовский силикатный завод, все — Россия, Забудова, Беларусь и др.)).
Исходные компоненты — цемент, известь, песок и вода (в зависимости от пропорции на выходе получается блочный бетон или силикат). Чтобы запустить процесс газообразования, в смесь добавляют алюминиевый порошок. В результате бурной реакции с участием «крылатого» металла, извести, цемента и воды выделяется газ и, как следствие, образуются поровые клетки.
Полуфабрикат из газобетона отправляется в автоклав, где в тепличных условиях материал без деформаций и деформаций укрепляется и набирает прочность.Газобетонные блоки идеальной формы без единого изъяна упаковываются в плотный полиэтилен и отправляются по назначению.
В комплект поставки, помимо обычных товаров, могут входить специальные «фишки», например, «лотки» для перемычек, «фигурные» элементы сборно-монолитных потолков и т. Д.
Качество таких изделий находится на высшем уровне, а иначе и быть не может, ведь прочность и другие параметры контролируются автоматически на всех этапах технологического процесса.
Кладка из блоков — как в кино
Прекрасно смотрятся светло-серые, почти белые, газобетонные блоки. Поверхность изделий имеет водоотталкивающие свойства (за счет закрытых пор), то есть погодные условия на кладке не сказываются. Идеальная геометрия позволяет укладывать блоки на специальный минеральный клей, а не на цементно-песчаный раствор.
Таким образом, толщина швов кладки уменьшается до 3 мм (вместо 12-15 мм — норма для стандартной кирпичной кладки).Главное достоинство этих аккуратных «шовчиков» — исключение теплопроводных включений в теплой блочной кладке (обычные цементные швы хорошо проводят тепло). В эстетической привлекательности домов из газоблоков отказать нельзя.
Даже сам процесс строительства вызывает невольное восхищение — так дивны стены из безупречных серебристых камней. Правда, блочные дома редко остаются без отделки фасада. Самый простой вариант — штукатурка с последующим нанесением декоративного покрытия (атмосферостойкая краска, рельефная штукатурка, искусственный камень, керамическая плитка и т. Д.).
В качестве черновой отделки используют так называемые «теплые» изделия, то есть штукатурные смеси со специальными добавками, обеспечивающими выравнивающий слой повышенной теплоизоляционной способностью. Надо сказать, что газобетонные блоки отличаются хорошей адгезией к отделочным материалам. Внутри стены обычно выравнивают гипсовой штукатуркой (во влажных помещениях — цементной), что способствует энергосбережению ограждающих конструкций.
Демократия в походе
Если вы планируете построить в садовом товариществе гараж, флигель или летнюю кухню на шесть соток, то для подобной конструкции лучше всего подойдет пенобетон.Его главное и единственное преимущество перед газобетонными блоками — более доступная цена. В остальном «пенопласт» уступает своему «близкому родственнику».
Пеноблоки производят на простом оборудовании. Специальная установка может работать даже в полевых условиях. Заливается пенобетон во внутреннее пространство так называемой колодезной кирпичной кладки (к сожалению, сегодня этот способ практически не применяется).
Неудивительно, что пеноблоки — это прерогатива малого и среднего бизнеса.Все хорошо, но вывод часто отклоняется от требований технологической карты. Кроме того, в качестве пенообразователя используются органические вещества (побочные продукты кожевенной промышленности и др.), Срок хранения которых не бесконечен. Использование прошитого органического материала отрицательно сказывается на качестве материала. Однако даже в самом лучшем случае пеноблоки отличаются очень размытой прочностью и теплотехническими характеристиками.
Твердение «на открытом воздухе» вызывает усадку и внутреннее напряжение бетонных изделий.Геометрически блоки тоже не идеальны, что полностью исключает кладку стен на минеральный клей.
И, как уже было сказано, цементно-песчаные швы кладки — не что иное, как пресловутые мосты холода. Тем, кто все-таки решил построить коттедж для круглогодичного проживания из пеноблоков, необходимо предусмотреть установку той или иной системы утепления фасада.
Ссылка по теме: Бетон своими руками — составы и классы, виды и виды бетона
Тепловые капсулы
В состав полистиролбетона входят гранулы полистирола размером 0,5-35 мм, благодаря которым материал отлично сохраняет тепло (по теплотехническим параметрам опережает другие виды ячеистого бетона) и хорошо защищает корпус от шума, что особенно важно. для коттеджей, построенных возле железных и автомобильных дорог.
Блоки этого типа легче газо- и пенобетонных, что снижает транспортные расходы и облегчает работу каменщиков. Изделия из полистиролбетона устойчивы к влаге. Однако стены из таких блоков нуждаются во внешней отделке (точно так же, как и в интерьере), прежде всего для придания дому эстетически приемлемого вида. Кроме того, слой минеральной штукатурки увеличивает пожаробезопасность конструкции.
Дело в том, что пенополистиролбетон относится к горючим материалам (хотя и трудновоспламеняющимся и самозатухающим).Даже если стены не загорятся, от повышенной температуры произойдет разрушение гранул и, как следствие, ухудшится состояние ограждающих конструкций. И, наконец, дома из пеноблоков укрепляют монолитными железобетонными поясами, которые при всей своей мощности легко отводят тепло на улицу. Чтобы перекрыть эти «каналы», стены утепляют снаружи, то есть точно так же, как при строительстве из пеноблоков.
Читайте также: Дом из газобетона своими руками — арматурный утеплитель и вагонка
Отличные возможности
Современные системы утепления фасадов позволили расширить возможности малоэтажного домостроения и внедрить в него элементы прогрессивной технологии монолитного строительства.Другими словами, сначала под крышу кладут железобетонный каркас. F Затем параллельно производят различные виды строительно-монтажных и инженерных работ. Пространство между площадками монолитного строительства заполнено теплоизоляционными блоками из ячеистого бетона.
Снаружи устанавливается утеплитель и накладывается многослойная отделка фасада или навешивается защитный декоративный экран (две разные системы утепления мокрых фасадов и вентилируемого фасада).Внешний теплоизоляционный слой перекрывает теплопроводящие элементы каркасной конструкции.
Строительство идет ускоренными темпами. Под крышей, независимо от состояния внешних стен, прокладывают трубопроводы, устраивают межэтажные лестницы и многое другое.
© Автор: Татьяна Гагарина
ИНСТРУМЕНТЫ ДЛЯ МАСТЕРОВ И МАСТЕРОВ, ТОВАРЫ ДЛЯ ДОМА ОЧЕНЬ ДЕШЕВЫЕ. БЕСПЛАТНАЯ ДОСТАВКА. ЕСТЬ ОТЗЫВЫ.
Ниже другие записи по теме «Как сделать своими руками — домохозяину!»
Подписывайтесь на обновления в наших группах и делитесь.
Давай дружить!
Aac Машина для производства газобетонных блоков в автоклаве
Описание продукта
О блоке AAC:
что такое блок AAc? Изготовлен из цемента, извести, летучей золы и песка, гипса … и закончен паровым отверждением.Он обладает такими характеристиками, как: легкий вес, экономия затрат, сейсмостойкость, высокая прочность, водонепроницаемость, сохранение тепла, теплоизоляция, звукоизоляция, экономия ресурсов … Блок AAC, как новый строительный материал, уже много лет изготавливается и применяется в Китае, и теперь Hngfa имеет полный опыт в производстве машин и блоков AAC…
Две точки о AAC:
1. легкий вес. Плотность обработанного бетона обычно составляет 400-700 кг / м3 (в зависимости от рынка продукции), такая же, как 1/3 глиняного блока и 1/5 Обычный бетон.Таким образом, использование светового блока может снизить вес конструкции, а также лучше всего уменьшить балку крыши и опоры колонны. тогда вы можете видеть, что это может сэкономить материал и стоимость, а также бороться с тряской.
2. температура хранения. Он имеет много пористых материалов, коэффициент сердечного ритма подачи равен 0.9-0,22 Вт / (мк), то же, что 1/4 или 1/5 глиняного кирпича, поэтому сейчас это лучшие материалы в мире.
Пропорция сырья блока AAC:
A. Цемент, известь, газообразный блок из летучей золы Пропорция сырья | B. цемент, известь, песчаный газовый блок-сырец Пропорция материала | ||||
Наименование | Единица | Пропорция | Наименование | Единица | Пропорция |
Зола уноса | % | 65-70 | Песок | % | 55-65 |
Цемент | % | 6-15 | Цемент | % | 10-20 |
Известь | % 9 0041 | 18-25 | Известь | % | 20-30 |
Гипс | % | 3-5 | Гипс | % | 2-3 |
Алюминиевая порошковая паста (600 кг / м³) | 1/10000 | 8 | Алюминиевая порошковая паста (600 кг / м³) | 1/10000 | 8 |
Расход воды и материалов | 0.60-0,65 | Расход воды и материала | 0,65-0,75 | ||
Система литья | ° c | 36-40 | Система литья | ° c | 35-38 |
Время смешивания алюминия | с | 30-40 | Время смешивания алюминия | с | 30-40 |
000
Отправить запрос <<
Приложение AACBlock
Преимущества приложения AAC Brock:
1.Звукоизоляция: стена
AAC имеет отличный класс передачи звука (STC), рейтинг 44. Результат: Практически звукоизолированные интерьеры.
2. Теплоизоляция:
Обладает самым высоким термическим рейтингом в отрасли… .R30! Таким образом обеспечивается хорошая теплоизоляция помещений, предотвращая попадание теплого воздуха летом и холодного воздуха зимой. AAC снижает стоимость кондиционирования воздуха на 30%.
3. Сейсмостойкость:
Силы землетрясения, действующие на конструкцию, пропорциональны весу здания, поэтому AAC демонстрирует отличную устойчивость к силам землетрясений.В регионах с высокой сейсмической активностью, таких как Япония, используется исключительно AAC. Доказано, что он выдерживает ветровые нагрузки тропических штормов 5 категории.
4. Площадь пола:
Использование более тонких блоков (6 дюймов вместо 9 дюймов внешних стен) из-за их отличных водонепроницаемых и изоляционных свойств приводит к увеличению площади пола на 3-5%.
5. Экономия затрат:
Легкость AAC значительно снижает собственный вес здания, что приводит к снижению стоимости конструкции из стали (до 27%) и цемента (до 20%).Стены из AAC, в 8 раз превышающие размер глиняного кирпича, включают 1/3 швов, таким образом, общая экономия раствора составляет до 66%.
Его автоматический производственный процесс дает AAC исключительную точность размеров и гладкие поверхности, устраняя необходимость в трехслойной штукатурке стен и позволяет наносить окончательный слой 6 мм (шпатлевка / POP).
6. Огнестойкость:
Лучшая в своем классе степень огнестойкости 4 часа. Температура плавления AAC составляет более 1600 ºC, что более чем в два раза превышает типичную температуру 650 ºC при пожаре в здании.
7. Термиты, устойчивые к вредителям, ненавидят AAC:
Изготовленный из неорганических минералов, он не способствует росту плесени.
8. Водный барьер:
Его структура не допускает капиллярного действия, что делает его непроницаемым для воды. Его водонепроницаемые свойства дополнительно улучшаются за счет добавления добавок на основе силикона.
Соотношение прочности и веса выше, чем у бетона M150, и намного превосходит требования индийских строительных норм.
9. Энергоэффективность:
AAC — это 100% экологичный строительный материал и предпочтительный материал для стен в зданиях, сертифицированных по стандарту LEED (центр ITC, экологичное строительство с самым высоким рейтингом было построено с использованием AAC).AAC является наиболее энергоэффективным и ресурсоэффективным в том смысле, что он использует наименьшее количество энергии и материалов на 1 м³ продукта. В отличие от процесса производства кирпича, в котором используется предыдущий верхний слой сельскохозяйственной почвы, в AAC используется летучая зола (65% веса), что обеспечивает наиболее конструктивное решение национальной проблемы утилизации летучей золы.
Газобетонный автоклавный блок — это легкий и пористый строительный материал:
A.Он может быть изготовлен из кирпича и стальных блоков любого размера: 600 * 200 * 100 мм, 80 * 80 * 180 мм, 240 * 115 * 53 мм, 600 * 200 * 125 мм и т. Д. Их можно использовать в промышленном строительстве. и обычное здание. В будущем блок AAC станет идеальной заменой традиционному глиняному кирпичу.
Б. Производительность: от 50 000 м3 до 300 000 м 3 в год.
Наши услуги
1. Гарантийный период: 12 месяцев после завершения установки оборудования и послепродажное обслуживание в течение всего срока службы.
2. Установка: для производственной линии Hongfa отправит технических специалистов для установки машин и бесплатного обучения рабочих заказчика.
3.Технические услуги: бесплатный дизайн, бесплатная поддержка технологий, бесплатное планирование объекта.
Информация о компании
Guangxi Hongfa Heavy Machinery Co., Ltd расположена в промышленной зоне Илин в городе Наньнин, Гуанси, Китай, занимает площадь 60 000 м2, площадь здания 23000 м2 и имеет 24 старших инженера и инженера и 180 технических сотрудников.
Председатель правления, г-н Гао Чэнфа, наряду с персоналом и рабочими, тепло приветствует посещение и сотрудничество всех новых и старых клиентов.
FAQ
FAQ:
1. Как я могу доверять качеству оборудования?
Наши продукты прошли сертификацию ISO9001-2000 и CE, и мы производим машины в течение 27 лет с полным опытом, обновляя технические идеи и приложения. Кроме того, наши машины экспортируются в более чем 96 стран и всегда имеют хорошую репутацию у наших зарубежных клиентов. ,Мы полностью протестируем нашу продукцию перед отправкой, чтобы убедиться, что все оборудование работает нормально, когда оно попадет к вам в руки.
2. Когда вы доставляете товар?
Обычно через 20 дней после получения депозита и подтверждения от покупателя.
3. Как насчет оплаты?
30% как предоплата T / T, 70% как остаток, оплачиваемый T / T перед загрузкой (L / C также приемлем).
4. Включена ли форма в цену?
Да, указанная выше цена включает одну форму бесплатно, дополнительные формы оплачиваются в соответствии с дизайном.
По всем вопросам обращайтесь по телефону:
Bella Luo
Тел .: 00867715672282/6036912
Веб-сайт: www.gxhongfa.cn
Оборудование для производства блоков Aac из автоклавного пенобетона
Базовое введение:
Оборудование для производства блоков из автоклавного газобетона AAC
Автоклавный газобетон (AAC) — это кремнийсодержащий материал (песок, летучая зола и кремниевые хвосты, такие как отходы фарфоровой глины, отходы обработки камня, доменный шлак и т. Д.) И известковые материалы (известь, цемент) в качестве основного сырья. , смешивание жирного газообразного агента (алюминиевый порошок) по ингредиентам, смешивание, литье, предварительное поднятие, резка, автоклав, процесс отверждения из легких пористых силикатных продуктов, потому что волосы содержат много газа даже после небольших пор, следовательно название газобетона.
Процесс производства AAC
1. Ленточный конвейер | 2. Дозировочная машина | 3. Роликовый грохот | 4. Бак для жидкого навоза | 5. Шаровая мельница мокрого типа |
6. Щековая дробилка | 7. Средство для удаления пыли | 8. Ковшовый элеватор | 9. Силос для известкового камня | 10. Сухая шаровая мельница |
11.Силос для порошка извести | 12. Силос для цемента | 13. Винтовой конвейер | 14. Резервуар для хранения жидкого навоза | 15. Весы для жидкого навоза |
16. Весы для извести и цемента | 17. Паромная тележка | 18. Кран опрокидывающийся | 19. Режущий станок | 20. Станок для резки |
21. Опрокидывающийся кран | 22. Паровая тележка | 23. Автоклав | 24. Кран после автоклава | 25.Продуктовый кран |
26. Боковой пластинчатый конвейер |
Преимущество AAC:
- Легкий : Пористость достигает от 70% до 85%, объемная плотность обычно составляет 500 ~ 900 кг / м3, поскольку 1/5 обычного бетона, 1/4 глины, 1/3 пустотелого кирпича и тому подобное с деревом могут плавать в воде. Это может снизить вес здания, снизить стоимость интегрированного здания.
- Огнестойкость : Большая часть основного сырья — неорганические материалы, поэтому оно обладает хорошей огнестойкостью и не выделяет вредных газов при пожаре. Огонь 650 градусов, как огнеупорный материал, толщина стен 90 мм может достигать 245 минут огнестойкости, 300 мм толщина стены может достигать 520 минут огнестойкости.
- Звукоизоляция : Благодаря уникальной пористой структуре он обладает звукопоглощающей способностью. Способность звукопоглощения может достигать стены толщиной 10 мм до 41 дБ.
- Изоляция : Поскольку материал внутри имеет большое количество пор и пористость, что имеет хорошие теплоизоляционные свойства. Коэффициент теплопроводности составляет 0,11-0,16 Вт / МК, как 1 / 4-1 / 5 кирпича. Обычно изоляционный эффект от стены из пенобетона толщиной 20 см эквивалентен обычной кирпичной стене толщиной 49 см.
- Проницаемость : Результат материала благодаря составу множества независимых мелких пор, поглощение влаги медленное, в объеме абсорбента в 5 раз больше, чем насыщение глины.При использовании в ванной, стена может быть обработана непосредственно на стыке клеевой плитки.
- Антисейсмический: Та же самая структура здания, улучшает два сейсмических уровня, чем уровень кирпича.
- Зеленый : Производство, транспортировка, все используют процесс загрязнения, для защиты пахотных земель, экономии энергии, является одним из видов зеленого строительного материала.
- Долговечность : прочность материала — это стабильность в образцах, испытанных после одного года атмосферного воздействия; интенсивность увеличилась на 25% и оставалась стабильной через десять лет.
- Ярлык : обладает хорошей обрабатываемостью, его можно распиливать, строгать, сверлить, забивать гвоздями и подходит для приклеивания клеящего материала, что создает благоприятные условия для строительства.
- Экономия : Интегрированная более низкая стоимость, чем при использовании более 5% полнотелого глиняного кирпича, и может увеличить полезную площадь, значительно улучшить использование площади пола.
Требования к сырью:
1 | Песок | JC / T622-1996 | ||||||
Отличный товар | Первоклассные товары | Квалифицированный товар | ||||||
SiO2 | диоксид кремния | ≥ | 85% | 75% | 65% | |||
K2O + Na2O | калия + оксид натрия | ≤ | 1.50% | 3,00% | 5,00% | |||
SO3 | трехокись серы | ≤ | 1,00% | 2,00% | ||||
глина | ≤ | 3,00% | 5,00% | 8,00% | ||||
водное соотношение | ≤ | 8,00% | ||||||
карбонат кальция (коралл, зель и др.) | ≤ | 10.00% | ||||||
примеси (кора, корни) | НЕТ | |||||||
2 | Летучая мышь | JC409-91 | ||||||
Отличный товар | Первоклассные товары | Квалифицированный товар | ||||||
Finess (квадратный экран 0,045 мм слева) | ≤ | 30% | 45% | 55% | ||||
Потребность в воде нормальной консистенции | ≤ | 50% | 58% | 60% | ||||
Потери при возгорании | ≤ | 7% | 12% | 15% | ||||
SiO2 | ≥ | 40% | 40% | 40% | ||||
SO3 | ≥ | 2% | 2% | 2% | ||||
3 | Лайм | JC / T621-1996 | ||||||
Отличный товар | Первоклассные товары | Квалифицированный товар | ||||||
А (CaO + MgO) | Кальций доступный | ≥ | 90% | 75% | 0.65 | |||
MgO | магнезия | ≤ | 2% | 5% | 8% | |||
SiO2 | диоксид кремния | ≤ | ||||||
CO2 | двуокись углерода | ≤ | 0,07 | |||||
скорость дегестации мин | ≤ | 5–15 | ||||||
температура дегестации ℃ | ≥ | 60–90 | ||||||
непереваренный остаток | ≤ | 5% | 10% | 0.15 | ||||
Тонкость готовой продукции (остаток выше сита 0,08 мм) | ≤ | 10% | 15% | 0,2 | ||||
4 | Цемент | ГБ175-1999 | ||||||
Химический состав | ||||||||
SiO2 | диоксид кремния | 21-23% | ||||||
Al2O3 | полуторный оксид алюминия | 5-7% | ||||||
Fe2O3 | полуторный оксид железа | 3-5% | ||||||
CaO | оксид кальция | 64-48% | ||||||
MgO | магнезия | 4-5% | ||||||
5 | Алюминиевая пудра | JC407-2000 | ||||||
Тип | Код | Содержание твердых веществ | Алюминий активированный в твердых телах | Скорость вспенивания (%) | ||||
≥ | ≥ | 4 мин. | 16 минут | 30 минут | ||||
Состав на масляной основе | GLY-75 | 75% | 90% | 50-80% | 90% | 99% | ||
GLY-65 | 65% | |||||||
Состав на водной основе | GLS-70 | 70% | 85% | 40-60% | ||||
GLS-65 | 65% |
Основное оборудование производственной линии AAC:
- Фрезерное оборудование:
а.Дробилка: Известь, гипс и другие сыпучие материалы необходимо измельчить на первом этапе установки AAC.
г. Миллер: Материал AAC должен быть полностью измельчен, чтобы улучшить реакцию. Шаровая мельница широко используется, бывает двух типов: сухая и мокрая, может быть выбрана по запросу.
- Оборудование для дозирования материалов: Автоматическая система дозирования с компьютерным управлением обычно используется для измерения сырья.
- Оборудование для смешивания и литья материалов: Смеситель, это машина для смешивания суспензии, а также машина для литья суспензии.
- Режущий станок: Заготовка AAC формируется после литья и предварительного отверждения, так как размер слишком большой, ее необходимо разрезать для получения продукта требуемого размера.
- Автоклав: Автоклав — это устройство для получения силикатных продуктов гидратации физико-механических свойств.
- Котел: котел поддерживает автоклав, печь предварительного нагрева и другие объекты с теплом.
а. Рама пресс-формы, дно пресс-формы и тележка для пресс-формы — они составлены вместе, чтобы сформировать литейную форму, которая является основным формовочным оборудованием на производственной линии AAC.
г. Тележка для закалки, тележка для парома и вешалки, они должны быть оборудованы в качестве вспомогательного оборудования в системе автоклавного отверждения.
г.Разделитель блоков. Сепаратор — это специальная машина, функция которой заключается в разделении пластикового блока на части для транспортировки и использования.
г. Упаковочная машина для блоков.
,